NASA’s Space Launch System will be the most powerful rocket we’ve ever built. When completed, SLS will enable astronauts to begin their journey to explore destinations far into the solar system.
Over the past few months NASA has been hard at work moving and assembling the largest pieces of structural test hardware for America’s new deep space rocket, the Space Launch System. It was loaded into Test Stand 4693 at NASA’s Marshall Space Flight Center in Huntsville. The liquid hydrogen tank is part of the rocket’s core stage that is more than 200 feet tall with a diameter of 27.6 feet, and stores cryogenic liquid hydrogen and liquid oxygen that will feed the vehicle’s RS-25 engines. The liquid hydrogen tank test article is structurally identical to the flight version of the tank that will comprise two-thirds of the core stage and hold 537,000 gallons of supercooled liquid hydrogen at minus 423 degrees Fahrenheit. Dozens of hydraulic cylinders in the 215-foot-tall test stand will push and pull the tank, subjecting it to the same stresses and loads it will endure during liftoff and flight.
Detailed below is a brief timeline of the assembly, transportation, and testing of the SLS rocket’s core stage along with the key elements Futuramic has built along the way.
July 5th, 2017 / via spaceflightinsider.com
NASA MOVES TOWARD SLS STRUCTURAL TESTING AT MARSHALL
“Moving beyond site selection controversy and production problems that caused headlines in May, NASA is working to complete a Space Launch System (SLS) structural test article at the Space Agency’s Michoud Assembly Facility (MAF) in Louisiana.”
In the foreground we see the Dome Rounding and Break Over Tool designed, Built and Installed by Futuramic. This tool does as its name suggests. Precision rounds a dome then hands it off to the Vertical Assembly Center in either a upright orientation for the top of a LH2 or LOX tank or upside down for the bottom of either tank. The domes were made using a combination of the Segmented Ring Tool, Gore Weld Tool, Circumferential Weld Tool and Plug Welder all designed, built and installed by Futuramic.
July 19, 2018 / via nasa.gov
SPACE LAUNCH SYSTEM INTERTANK READIED FOR STRUCTURAL TESTING
“Engineers installed structural test hardware for NASA’s deep space rocket, the Space Launch System, into a test stand at NASA’s Marshall Space Flight Center in Huntsville, Alabama where testing recently began. The test version of the SLS intertank is being pushed, pulled and bent with millions of pounds of force to ensure it can withstand the forces of launch and ascent.”
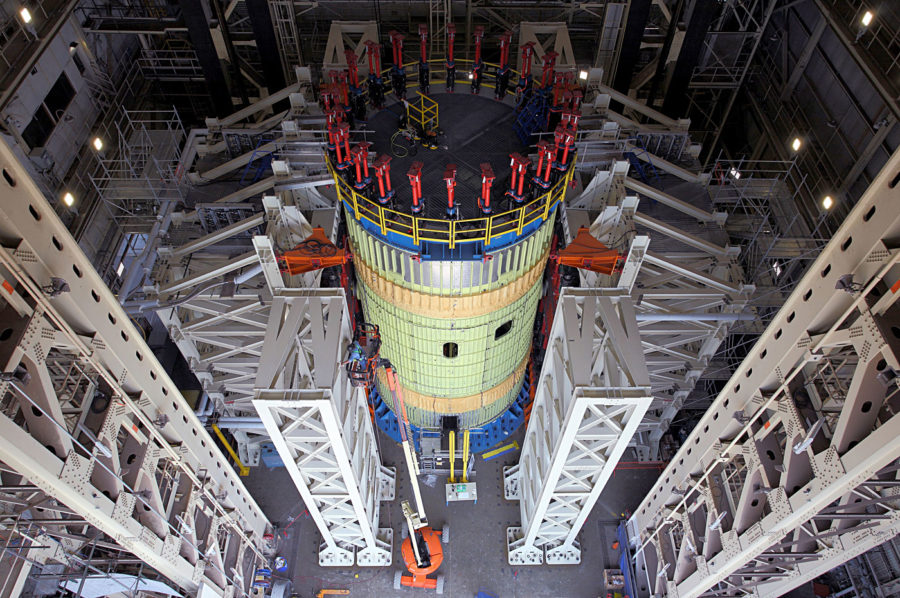
Futuramic built the simulators shown here in use during testing at MSFC.
Photo Credit: Todd Boles / NASA
Futuramic rebuilt the Space Shuttle intertank tooling to assemble the SLS Intertank . FTE also designed and built the tooling for assembling the Thrust Beam which is inside the Intertank. The thrust beam connects the top of the solid rocket boosters top to the core stage of the rocket.
Nov. 1, 2018 / via nasa.gov
INTERTANK FOR NASA’S NEW ROCKET READIED FOR FINAL ASSEMBLY
“Technicians lifted the intertank for NASA’s deep space rocket, the Space Launch System (SLS), into a vertical stacking area at NASA’s Michoud Assembly Facility in New Orleans. Here, engineers will join it with two other large structures to form the top half of the 212-foot-tall core stage that will be flown on Exploration Mission-1, the first flight of SLS and the Orion spacecraft.”

Intertank in a stacking cell being “Stacked”. Futuramic tooling was used to build the intertank.
Photo Credit: Jude Guidry / NASA
Dec. 12, 2018 / via nasa.gov
NASA INVITES MEDIA TO SEE LARGEST PIECE OF SLS TEST HARDWARE MOVE TO BARGE
“Media are invited to NASA’s rocket factory, the Michoud Assembly Facility in New Orleans, Friday morning Dec. 14, to view the largest piece of structural test hardware for America’s new deep space rocket, the Space Launch System. SLS will enable a new era of exploration beyond Earth’s orbit, launching astronauts in NASA’s Orion spacecraft on deep space exploration missions to the Moon and beyond.”
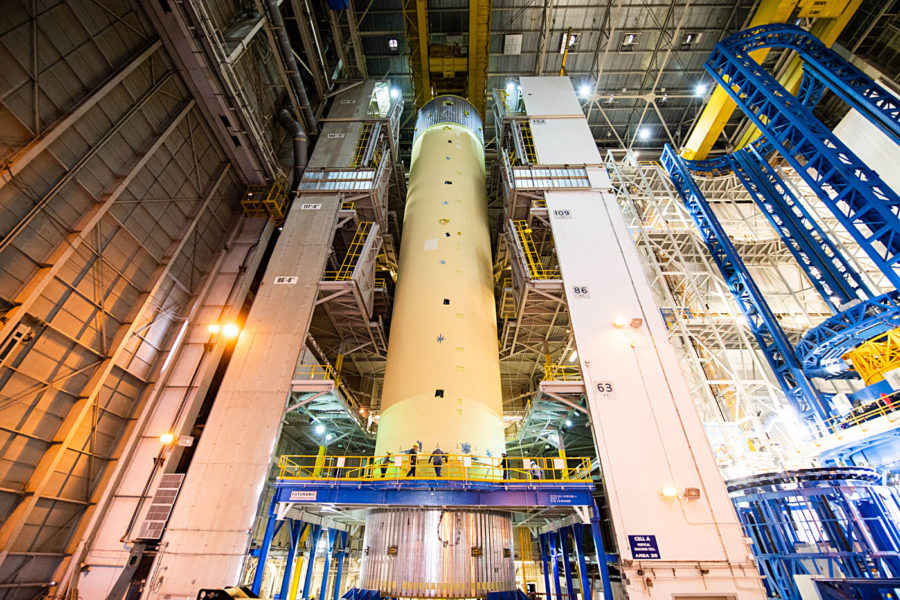
Cell A, the removable blue platform was designed and built by Futuramic. This is to modify the cell from Space Shuttle use to SLS.
Photo Credit: Todd Boles / NASA
December 14, 2018 / via windsorstar.com
NASA MOVES LIQUID HYDROGEN TANK TO HUNTSVILLE FOR TESTING
“NEW ORLEANS — NASA is moving a massive liquid hydrogen tank to Huntsville, Alabama, for testing as part of its plans to eventually return to the moon.”
Dec. 14, 2018 / via nasa.gov
LARGEST PIECE OF SLS ROCKET TEST HARDWARE MOVED FOR TESTING
“Technicians at NASA’s Michoud Assembly Facility in New Orleans, moved the largest piece of structural test hardware for America’s new deep space rocket, the Space Launch System, from the factory to the dock where it was loaded onto NASA’s barge Pegasus Dec. 14, 2018. The liquid hydrogen tank test article will make its way up the river to NASA’s Marshall Space Flight Center in Huntsville, Alabama, where dozens of hydraulic cylinders in Test Stand 4693 will push and pull on the giant tank, subjecting it to the same stresses and loads it will endure during liftoff and flight.”
Futuramic designed and built the tooling
- SRT, GWT, CDWT, PWT to make the domes for the ends of the LH2 tank
- Dome Rounding and Break Over Tool to hand off the dome to the Vertical Assembly Center
- Tank Rotation Stand for inspection and installing internal baffles
- Work Cells for applying the SOFI ( Spray on Foam Insulation)
The domes are covered by the simulators. FTE also built one of the simulators.
Jan. 15, 2019 / via nasa.gov
SLS LIQUID HYDROGEN TANK TEST ARTICLE LOADED INTO TEST STAND
“The largest piece of structural test hardware for America’s new deep space rocket, the Space Launch System, was loaded into Test Stand 4693 at NASA’s Marshall Space Flight Center in Huntsville, Alabama Jan. 14, 2019. The liquid hydrogen tank is part of the rocket’s core stage that is more than 200 feet tall with a diameter of 27.6 feet, and stores cryogenic liquid hydrogen and liquid oxygen that will feed the vehicle’s RS-25 engines.”
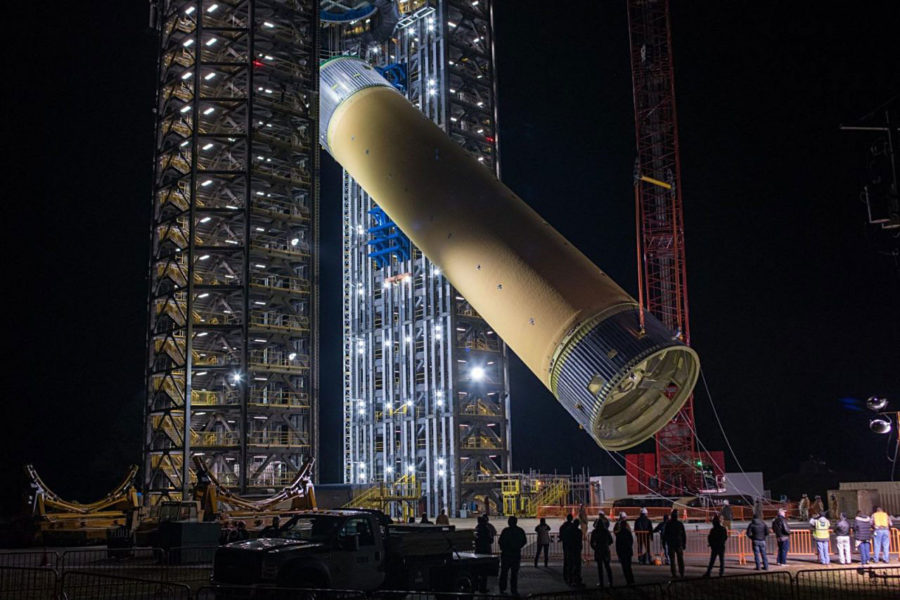
LH@ tank which has two domes made on multiple Futuramic designed, built and installed tools and on the top and bottom of the LH2 tank are the Intertank and Engine Section Structural simulator built by Futuramic.
Photo Credit: Tyler Martin / NASA
Jan 18, 2019 / via spaceflightinsider.com
SLS LIQUID HYDROGEN TANK TEST ARTICLE PLACED ON TEST STAND
“The structural test article for the Space Launch System’s liquid hydrogen tank is loaded onto Test Stand 4693 at NASA’s Marshall Space Flight Center in Huntsville, Alabama. Photo Credit: Tyler Martin / NASA”